| Our Process
Collect Valves from Customers specified Shop for transport to our facilities
Dismantle the Valves for visual inspection of Major Damage, Valve plate breakage, excessive wear etc.
Mark Valves individually with Job Numbers and Serial Number.
Degrease all components that will be re-used for the Reconditioned Valve.
Sandblast all components with a glass bead media to obtain a clean and rust free surface finish.
Check for non-visual cracks in the Seats, Guards and Damping plates by Observation under ultraviolet light.
Seats, Guards & centre bolts, if found cracked or damaged beyond repair will be replaced.
Preparation of Inspection report and quotation.
Machining, Grinding and/or Lapping the Valve Seat to obtain original tolerances and flatness.
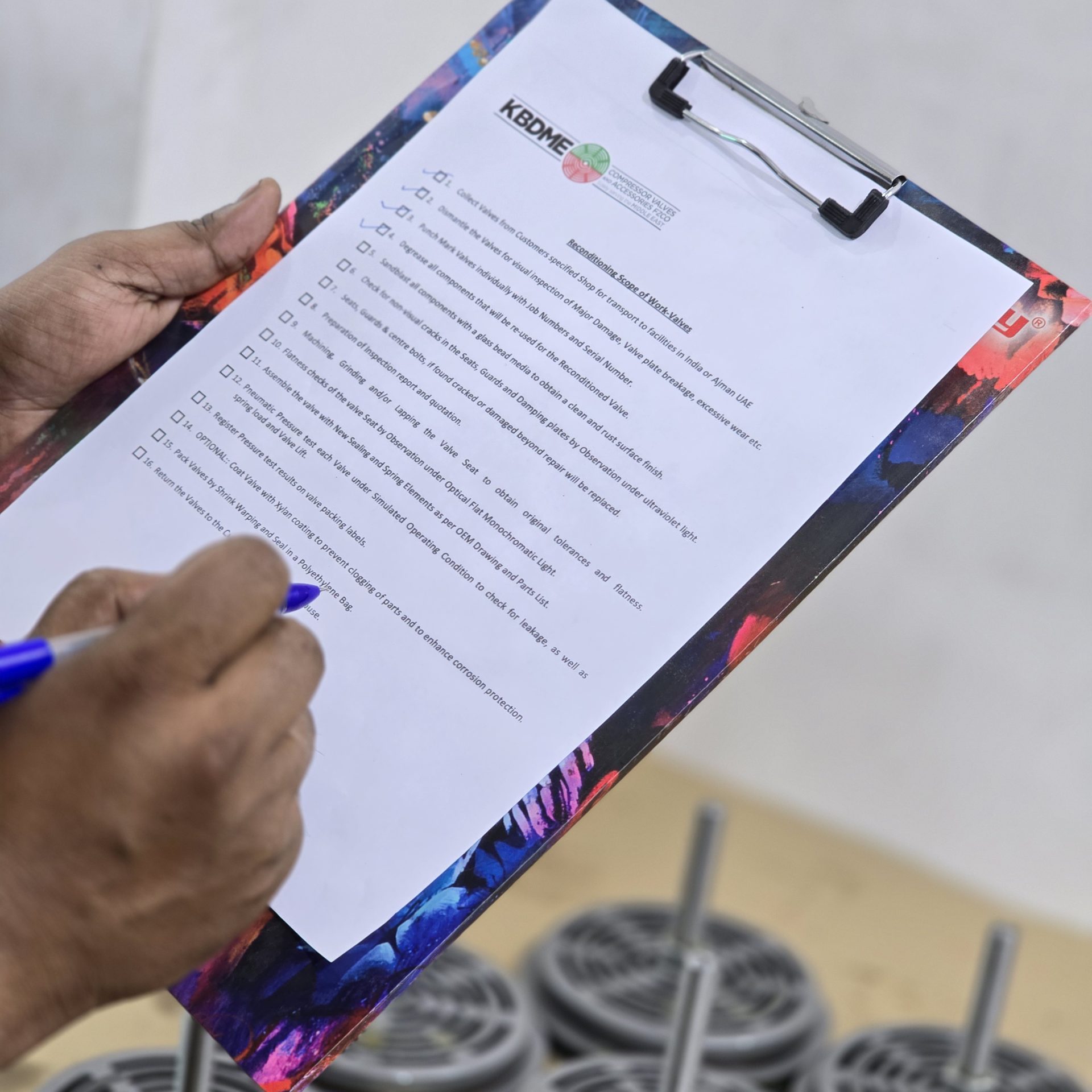
Flatness checks of the valve Seat.
Assemble the valve with New Sealing and Spring Elements as per OEM Drawing and Parts List.
Pneumatic Pressure test each Valve under Simulated Operating Condition to check for leakage, as well as spring load and Valve Lift.
Register Pressure test results on valve packing labels.
OPTIONAL: Coat Valve with Xylan coating to prevent clogging of parts and to enhance corrosion protection.
Pack Valves by Shrink Warping and Seal in a Polyethylene Bag.
Return the Valves to the Customers Specified Warehouse.